5 Types of Aluminium Casting and Their Uses
| 4:31 am
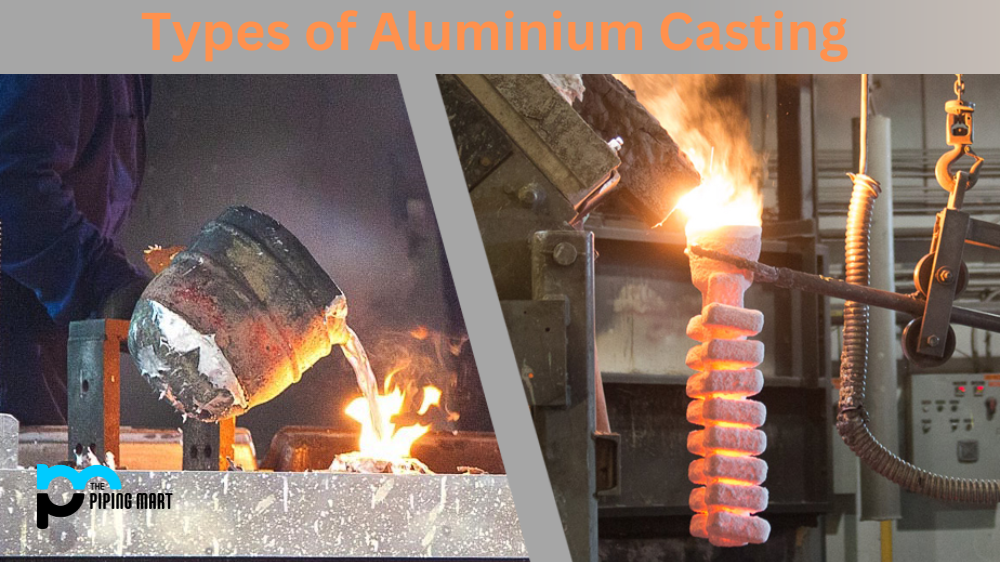
Aluminium casting can be complex, with different methods to accomplish the end goal. Each technique comes with its unique advantages and disadvantages. Due to the need for specific features, finishes, and overall quality, it’s crucial to understand the types of aluminium casting processes available. This blog will explore the different kinds of aluminium casting processes to help you decide the best choice for your project.
Sand Casting
Sand casting is the most common aluminium casting method globally, thanks to its versatility in creating simple or complex designs. This process involves creating a mould by packing sand around a pattern and waiting for the sand mould to harden before pouring the molten metal. Generally, sand casting is relatively cheap, effective, and can produce large parts quickly. Additionally, it enables the use of various alloys and metals. However, sand casting typically results in poor surface finishes and dimensional accuracy, which may require additional operations.
Die Casting
Die casting involves injecting molten aluminium into a mould or die to create the end product. This process requires precision and ensures excellent dimensional accuracy, thin walls and intricate features. Moreover, it yields exceptional surface finishes and produces parts that can be used without further operations. Die casting is commonly used in small component production, such as automotive, household appliances, and electronic devices. Nevertheless, the costs, including tooling and machinery, make die casting relatively expensive for small and one-off projects.
Permanent Mold Casting
Permanent mould casting or gravity die casting, is a semi-permanent metal casting process. It involves using reusable moulds made from iron, steel, or graphite, resulting in excellent surface finishes and tolerances. In this process, molten metal is poured into a reusable mould, and then the casting must cool and solidify before removal. Permanent mould casting is typically used for mid to high-volume production of complex parts, such as gears, pumps, and engine components. However, permanent mould casting requires upfront investment in tooling and production, making it relatively expensive.
Investment Casting
Investment casting is a process that involves the use of a wax pattern to create a mould that is later filled with molten metal. This process typically results in accurate and intricate parts with excellent surface finishes. Investment casting is known for producing parts that require minimal post-casting operations, which saves time and cost—typically used when small quantities of components are needed and where dimensional accuracy is critical, such as jewellery, dental appliances, and aerospace components.
However, the production of wax moulds and their removal from the casting can add to the cost of the process.
Plaster Casting
Plaster casting creates accurate and intricate parts with excellent surface finishes. This process involves using plaster of Paris to create a mould or pattern that is then filled with molten metal. Plaster casting is typically used for short production runs or for quickly creating parts with high accuracy. Although this method is unsuitable for large or heavy industrial castings, plaster casting allows for relatively inexpensive production of high-quality components that meet the necessary standards.
Conclusion
Aluminium casting processes are crucial in producing various components and parts used in multiple industries. Each method comes with unique advantages and disadvantages based on the complexity of the design, tolerances, quantity of parts, and overall quality needed. Understanding the different types of aluminium casting processes will help you choose the best option for your project. Whether you need sand casting for large-scale production, die casting for part precision, permanent mould casting for complex parts, investment casting for low volume and intricate details, or plaster casting for small, high-quality runs, choosing the proper aluminium casting process is an essential step towards achieving the desired results.

Meet Bhavesh, a seasoned blogger with a wealth of knowledge and experience. From metal products manufacturing to retail, Bhavesh has a diverse background in various industries and is dedicated to sharing his insights and expertise with readers.